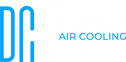
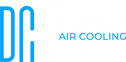

Dynamic Air Cooling
The essence of Dynamic Air Cooling technology is the direct transformation of warm air into cold air through the use of gas-dynamic effects. The technology is based on the mixed universal cycle developed and patented by the authors of the technology.


The cycle combines two gas-dynamic and two thermodynamic processes:
adiabatic and isentropic air compression in the compressor;
adiabatic and isentropic expansion, cooling and acceleration of air in the working element;
isothermal selection of the kinetic energy of the air flow in the air turbine;
isobaric heating of air when removing heat from the cooled volume of the refrigerating chamber.
Compared to the traditional vapour compression technology:
DAC uses air instead of hydrofluorocarbons to transfer energy, thus eliminating hydrofluorocarbons as a source of global warming;
In DAC-based cooling, energy is removed from the air and then converted to electricity to help power the device, making it 30% more energy efficient than a traditional vapour compression AC/refrigeration system. In traditional cooling units, this energy is wasted;
Due to a simpler design and smaller form factor, manufacturing costs of DAC devices can be 30% lower compared to traditional HFC-based units of similar cooling capacity.






Uniqueness of our approach
Most traditional cooling devices are based solely on the principle of adiabatic gas compression and gas expansion. This means they take advantage of the fact that a gas heats up when compressed and cools down when expanded. DAC uses a different approach – we base our technology on the principle of energy conversion and recuperation. This happens when one converts the heat energy contained in a gas (as defined by the temperature of the gas) into kinetic energy (the speed of air movement). This kinetic energy is then used to generate electricity which is next transferred out of the system, resulting in an overall decrease of system energy. This then results in highly effective cooling. Our team of experts created a mathematical model of this energy transformation process and utilized it to develop the operating basis of DAC technology prototypes.
A somewhat similar physical principle based on the Joule-Thomson effect is currently used in air chillers and turbo expanders. However these solutions have significant limitations: they use a very high operating pressure of 40-50 bars (580 - 725 psi) and cooling is achieved via rapid pressure drop. This process requires expensive steel tanks and powerful electric motors which result in high material and electricity costs. As such, the Joule-Thomson process is not economically practical in the majority of cooling applications.
The key differentiating feature of DAC technology versus Joule-Thomson is that it achieves a very fast decrease in gas (air) temperature thanks not to a large pressure drop but due to an increase in gas kinetic energy. This process of accelerating gas flow is the essence of DAC know-how and is protected by several patents.
One indication of the superiority of the DAC cooling process is that it requires a maximum pressure of just 2 – 3 bars (29 - 43 psi). In practice this results in much lower material and energy costs.

Cooling parameters
1.4
Cooling coefficient
Air
Refrigerant
0
Direct CO2 emissions
0,7kW
Electrical energy required to generate 1 kW of cold at -20°C
-92°C
DAC technology can cool gases down -92C from their starting temperature
∞
DAC technology can be used to create refrigeration devices of any cooling capacity
First prototypes: Reefers and HVAC

DAC technology can be used in a wide range AC/refrigeration applications. The company is currently developing prototypes for two priority market segments - refrigerated transport (a standardized 5 kW cooling solution for shipping containers) and HVAC solutions (an entry level 9 kW solution for air-conditioners and water chillers). Future plans also foresee development of DAC units for large space refrigeration (e.g. food storage rooms with a cooling capacity of 50 kW).







DAC Technology Unique Selling Points (USPs) include:
Environmental Friendliness:
DAC systems do not use coolants or refrigerants that contribute to the greenhouse effect or destroy the ozone layer;
Do not use water;
Require less electric energy than even state-of-the-art vapor compression AC/refrigeration solutions in most operating scenarios.
OPEX and CAPEX Savings:
DAC units are up to 30% more energy-efficient than traditional AC/refrigeration systems yielding lower running costs;
Feature 30% - 40% lower CAPEX costs as a result of simpler construction and fewer parts;
Insure no risk of fines or negative PR for environmental damage;
DAC technology can be used to upgrade existing AC/refrigeration systems to reduce their operating costs.
Versatility:
DAC technology can be used to construct a full range of AC/refrigeration solutions in commercial, residential & industrial applications.
